|
ICAMPS - Integrated Computer Aided Mine Planning Software |
|
|
|
|
Call 740-596-1023 Today! |
|
|
|
|
ICAMPS MineSimU
Simulated Mining - Underground Mine Planning software |
|
|
|
|
MineSimU is used to create detailed tonnage reports and timing maps. It has daily scheduling and monthly scheduling. In MineSimU production and quality forecasts are specific to the area mined each time period, not long term average values. It gives accurate results, rapid computations and convenient editing features which allow the mine engineer to try numerous scenarios and find the best combination of operating practices and mine design. Based on training experience, a mining engineer can learn MineSimU and have his mine plan up and running within a day. After that the mining engineer can go back and try different scenarios within an hour or two.
MineSimU has a variety of reporting options. Reports can be printed directly from AutoCAD or exported to third party software like Excel and Report Writer. It has extensive Royalty Reports and a very flexible function to view and draw the timing maps allowing for solid fill, hatching, and various labeling options.
MineSimU has the ability to adjust the mining rate based on seam height, difficulty code, time periods, by area or by machine. It also allows for Shift Exceptions based on machine and month, or you can have shifts per day for the mining area, otherwise it uses the shifts per day in the calendar. |
|
|
|
|
Key features |
|
|
|
|
|
|
|
|
|
Geology Features |
|
|
|
|
The simulated mining module requires geological and quality data in order to compute the total material mined (raw tonnage), processed tonnage and raw or processed quality for each timing sequence.
ICAMPS accepts gridded seam models from QuickSurf or other geological modeling systems or a comma or space delimited ENZ (XYZ) file. Individual parameter grids are combined into a master grid which contains up to fourteen parameters. A master grid must be assigned to each mining area. ICAMPS has the capability to simulate mining with multiple grids concurrently; one mine plan drawing can reference up to twenty different master grids. This feature is especially useful for multi-seam mining or where the available data justifies one or more fine grids in part of the mine and course grids elsewhere.
MineSimU also has graphical grid editing and compositing functions. Where bore hole data is relatively sparse, coarse grids are typically used. But, where more information is available, such as a longwall panel after development, a segment of the coarse grid can be refined to a small increment and the grid node parameters can be graphically edited to reflect local anomalies.
|
|
|
|
|
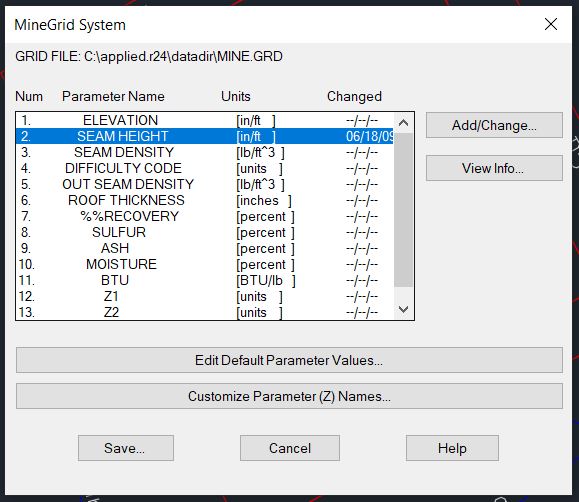 |
|
|
|
|
Adding and Editing grid parameters allows you to add and edit the grid parameters, set default values and more. |
|
|
|
|
|
|
|
|
|
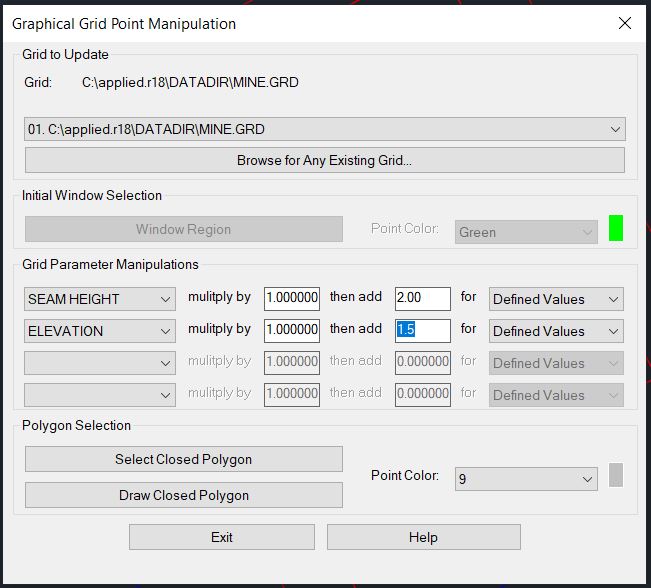 |
|
|
|
|
Graphical Grid Point Manipulation allows you to draw or select a polygon for points you want to change in the grid. |
|
|
|
|
|
|
|
|
|
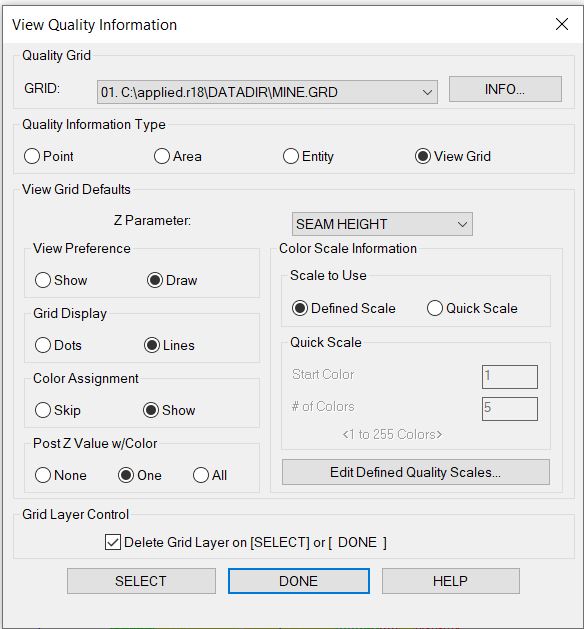 |
|
|
|
|
Viewing information about the grid lets you get grid info graphically or by selecting a region of the grid you want to see and you can define your own colors as below.It also has a quick scale that selects colors automatically. Selecting Area shows all the quality info as well as in-place raw tonnage and in-place clean tonnage for the area that you draw. |
|
|
|
|
|
|
|
|
|
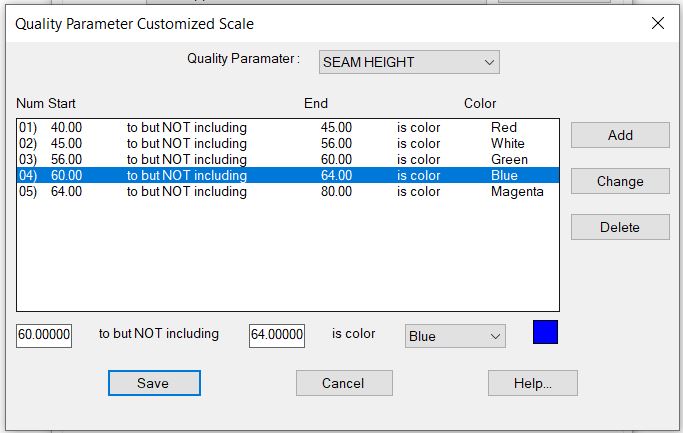 |
|
|
|
|
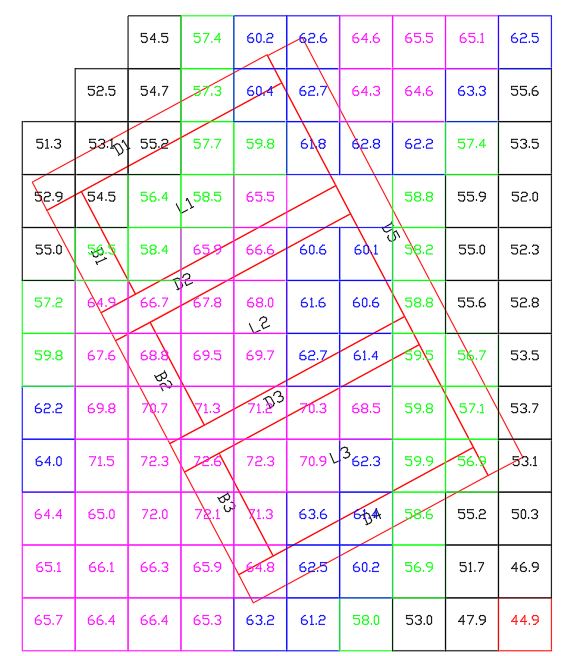 |
|
|
|
|
Above shows the grid created from View Quality with the colors specified. |
|
|
|
|
|
|
|
|
|
Where seam characteristics and equipment size require taking out-of-seam material, seam grids can be composited with the immediate roof and/or floor to reflect the actual quality of the shipped product.
Each grid can contain a difficulty code to reflect adverse mining conditions. This information is used to change the miner units productivity. Typically the geologist will outline problem zones on the seam map, and the planning engineer assigns the difficulty codes and productivity adjustment factors. Graphical grid editing is especially useful for creating difficulty code grids because the adverse conditions usually change abruptly and cannot be accurately represented with mathematical seam modeling techniques.
For overburden removal in surface mining, one of the grid parameters must be the overburden thickness. Where the deposit varies significantly in the vertical dimension and is thick enough to be removed in separate homogeneous layers or benches, each layer can have its own master grid. |
|
|
|
|
|
|
|
|
|
Calendar Features |
|
|
|
|
Each machine can have its own calendar. The calendars are created graphically from a standard wall calendar format. Non-working days that repeat each month, such as Saturdays and Sundays, are accounted for automatically. Non-working days which vary within and between years, such as holidays and vacation shutdowns, are picked individually or automatically using the Advanced button and Auto Button. The number of working shifts in each working day are also inserted in the calendar. Fractional shifts are allowed. You can also specify the number of hours worked per shift. |
|
|
|
|
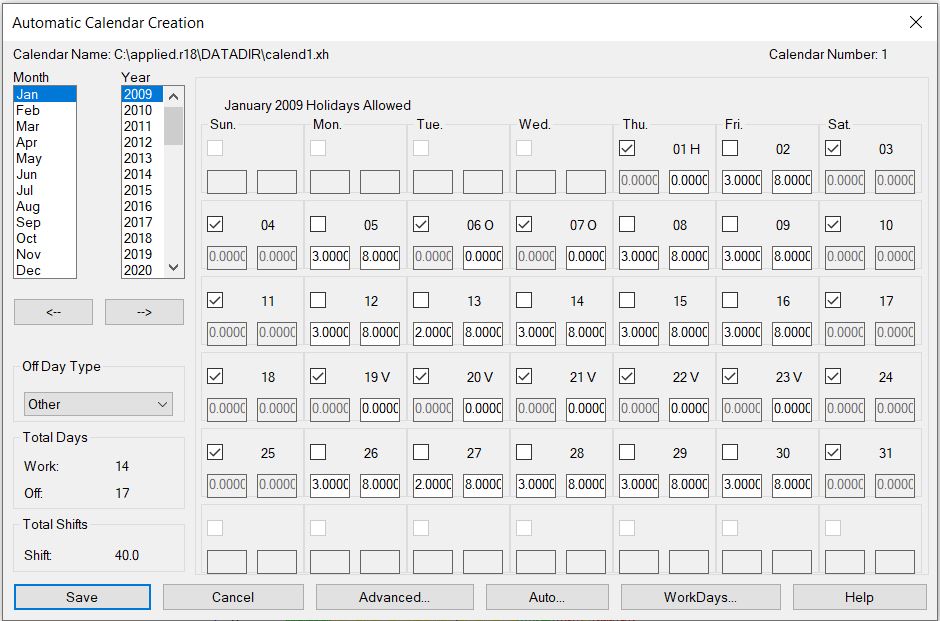 |
|
|
|
|
It can mark the days off by Normal, Vacation, Holiday or Other. Other than Normal it will put a V, H, O, or L (for Longwall Move CM Shutdown) next to the day number. |
|
|
|
|
|
|
|
|
|
The Advanced button allows you to automatically mark off days of the week and holidays over the entire span of the calendar or a specified time as shown below. The -1 for shifts means use the default. |
|
|
|
|
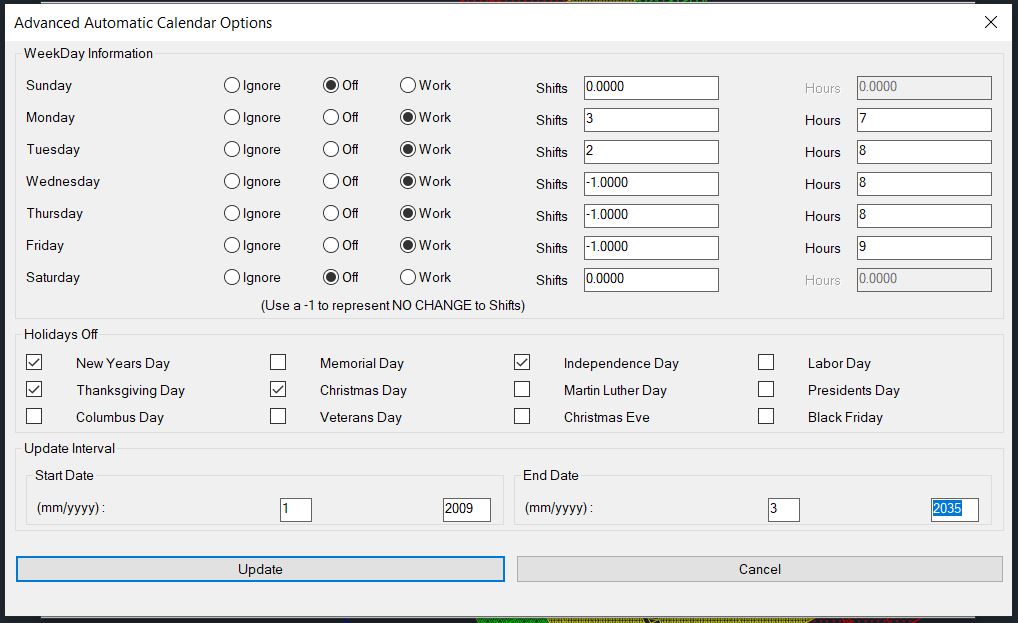 |
|
|
|
|
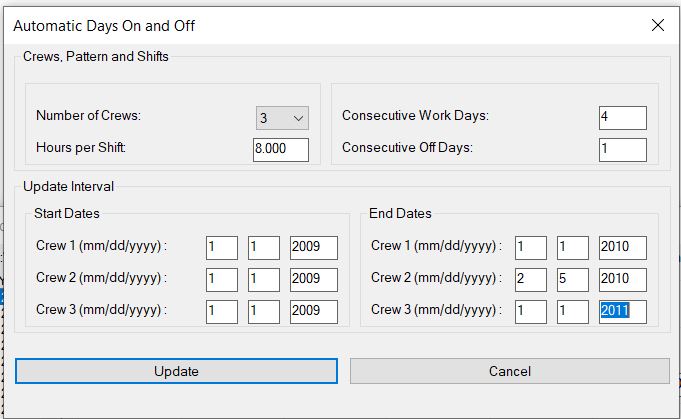 |
|
|
|
|
The above is how you can create a calendar by time for the consecutive days on and off. |
|
|
|
|
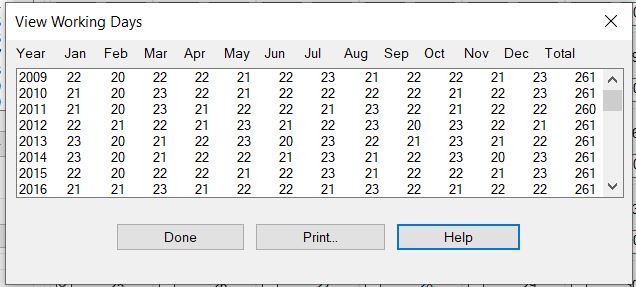 |
|
|
|
|
It can calculate the working days as shown above depending on the days off. |
|
|
|
|
|
|
|
|
|
AutoCAD Layout Features |
|
|
|
|
ICAMPS has two approaches to mine layout. One is to draw the mine layout using standard AutoCAD commands and later attach attribute blocks to each area. The other is to work inside the simulated mining module and use the special ICAMPS commands to draw mining areas or to create detailed projections including centerline drawings and pillar outlines.
The system can handle any reasonable mine layout. The mining areas are not limited to rectangular shapes. Designs can be retrieved from an existing drawing and copied to a new layout and repeated as necessary. The system allows the user to mirror, rotate, delete and reshape portions of existing layouts. The mine layout file can include symbols, identifying legends, text description and pointers to labor and material requirements files and other information that will affect mining costs. The figure below is an example of a mine layout containing both development and longwall panels. |
|
|
|
|
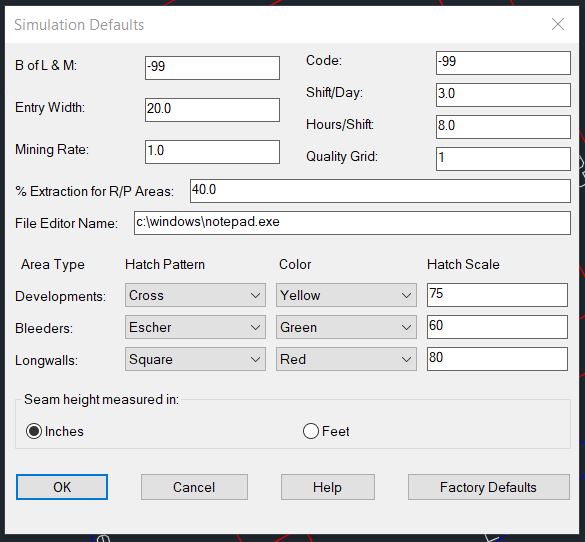 |
|
|
|
|
The Simulation Defaults allows you to set the defaults for mining areas as well the text editor you would like to use for viewing reports or making changes in an editor. It also tells the system if you are working in inches or feet for Seam Height. |
|
|
|
|
|
|
|
|
|
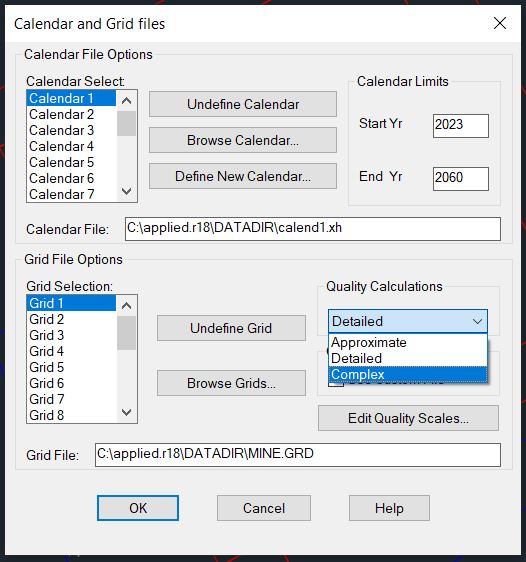 |
|
|
|
|
Set up the calendar and grid files. Calendar and grid files can be stored in a single or different folder/directory so you can use the same ones for different scenarios. |
|
|
|
|
|
|
|
|
|
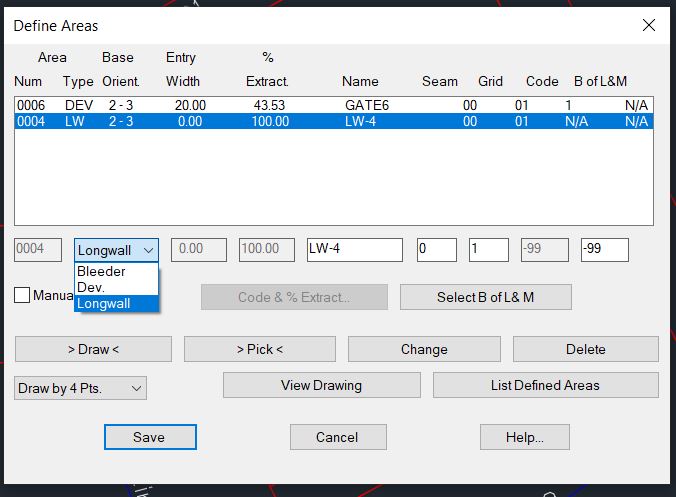 |
|
|
|
|
Define Areas lets you set up all the area info and mining direction as well as drawing by 2 points or 4 points and calculating the percent extraction.You may draw all your areas before hand with the menu options (Mining Area by 2 or 4 points) then just pick all of them all later in thie above dialog. Also you can use AutoCAD or your minemap and pick the areas. |
|
|
|
|
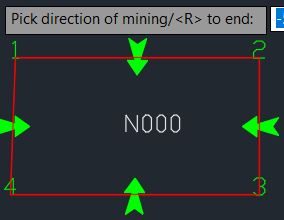 |
|
|
|
|
Picking the direction of mining is easy. The N000 will change to the the area type (B, D, or L) and the number assigned. For example L1, D5, B7 etc.. |
|
|
|
|
|
|
|
|
|
 |
|
|
|
|
You can pick Pillar Configuration and calculate the percent extraction. |
|
|
|
|
|
|
|
|
|
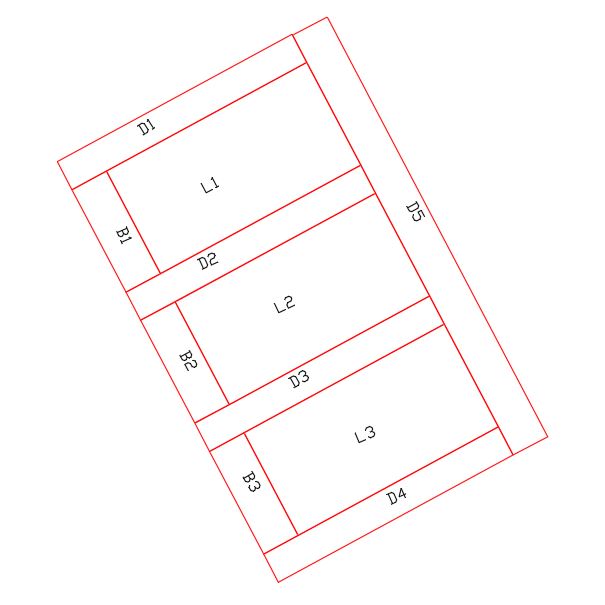 |
|
|
|
|
Above is a sample MineSimU drawing that comes with MineSimU. The letters designate the area type and user defined area number. For example L3 is Longwall area 3. They can be sequenced and/or mined in any order. |
|
|
|
|
|
|
|
|
|
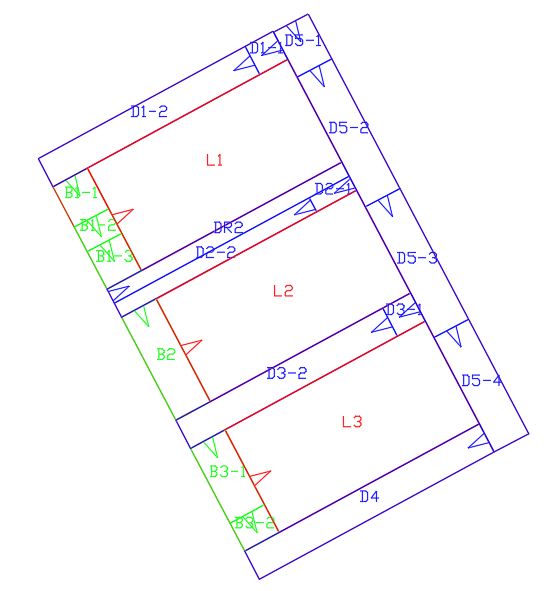 |
|
|
|
|
The above two images are a simple layout of defined longwalls, developments and bleeders. Areas can be subdivided and retreat mined. All layers can be turned on or off. |
|
|
|
|
|
|
|
|
|
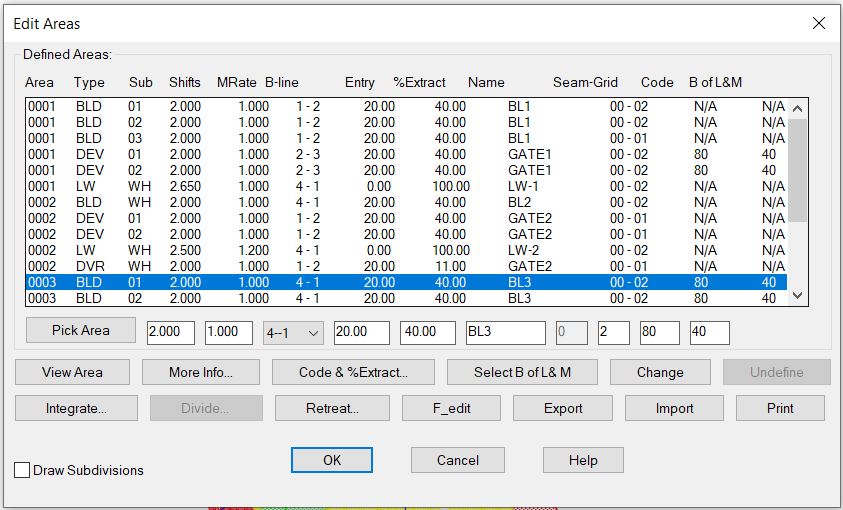 |
|
|
|
|
Edit Mining Area File lets you change any information about the selected mining area. The F-Edit allows you to make modifications in a text editor. |
|
|
|
|
|
|
|
|
|
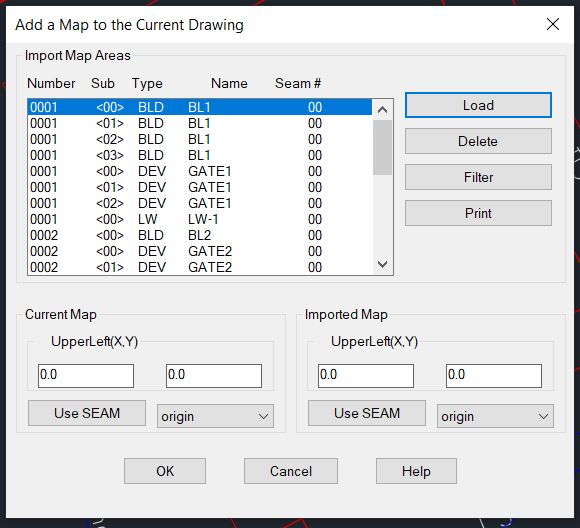 |
|
|
|
|
You can also add a MineSimU Map to your current drawing in case you need to combine maps or for any other reason. |
|
|
|
|
|
|
|
|
|
Where the mine operates in multiple seams, all the layouts for the individual seams are stored in one drawing. The seam layouts can be superimposed or they can be offset horizontally and/or vertically for a simultaneous unobstructed view of all the layouts. |
|
|
|
|
|
|
|
|
|
Sequencing Features |
|
|
|
|
The sequence in which areas are to be mined is an interactive process that involves the user and the ICAMPS system. To assign mining areas to a machine, the user points to the areas in the order they will be mined. Color coded graphical feedback lets the user see which areas have been assigned to a machine. The user also maintains the technological sequence of mining among the machines by assigning precedences where necessary. The simulator then follows the user specified mining sequence and precedence requirements and reports the duration and cause of any delays. |
|
|
|
|
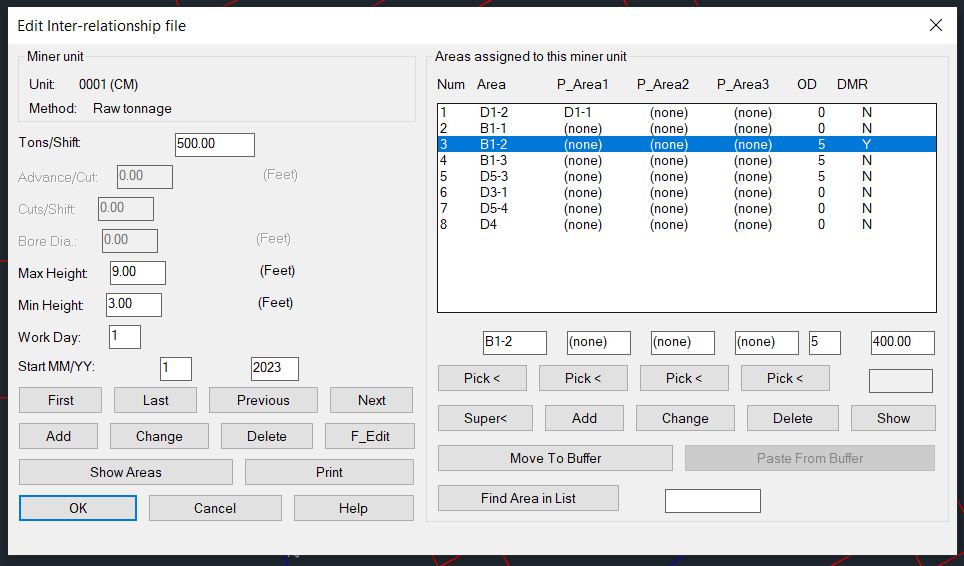 |
|
|
|
|
The above shows how mining areas are assigned to mining machines. The First, Last, Prev and Next allow you to move through the machines and the big list on the right shows the areas the machine will mine in order. The DMR means Different Mining Rate so that you can override the default mining rate for certain areas. |
|
|
|
|
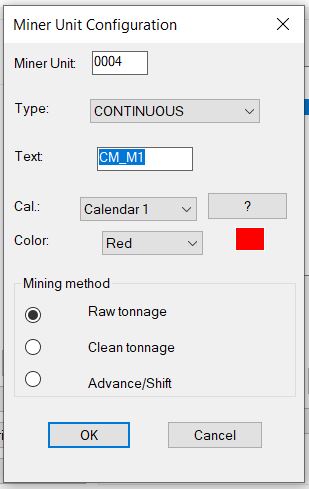 |
|
|
|
|
By clicking Add or Change in the Machine Sequence dialog you bring up the dialog box above. Here you can give the machine a unique number, select its type (continous, longwall,super-sect, minerborer, or roadheader), specify the calendar file it will use, the mining method and the color. |
|
|
|
|
|
|
|
|
|
Simulated Mining Features |
|
|
|
|
The system simulates mining with any combination of longwall, continuous/conventional miner, miner borer or roadheader. Each mining unit can have its own mining rate, either in tonnage or in linear advance. The tonnages per shift can be specified as total material remove or processed tonnage. Each miner unit can have its own calendar and production capacity. An exception routine allows the mining rate to vary from month to month. A mining area can be divided into subareas to allow more than one miner unit to work within an area and each mining area or sub-area can have its own mining rate. The system also allows the user to specify a time offset between areas for construction or to move equipment. The system has provisions to adjust the mining rate as a function of difficulty code and seam height.
The simulated production model computes the advance and average quality parameters per time period using an iterative process. The parameter estimates are exact weighted averages based on the proportion of each grid block within the area mined each period.
Most mine plans must be adjusted to meet budget requirements. Where longwalls provide the bulk of the production, the longwall schedule can be adjusted automatically by modifying the machine calendars and production rates until the target tonnage is achieved. Based on the longwall schedule, the system will adjust the development machine calendars to reflect the shifting of crews for longwall moves. The timing is then run for all machines. Normally the total tonnage will be within an acceptable margin of the budget requirements. If the schedule does not meet the tonnage criteria, the user can adjust the longwall targets and repeat the scheduling process.
|
|
|
|
|
|
|
|
|
|
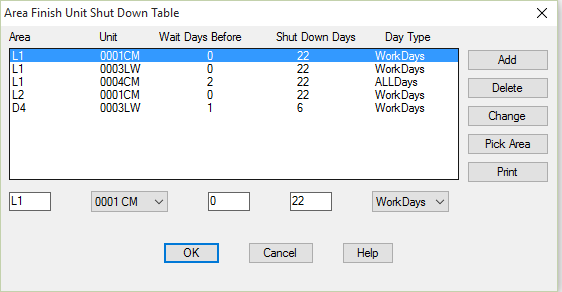 |
|
|
|
|
The Area Finish Unit Shutdown Table Above allows you to select areas on the minemap when that area finishes you can select the machine that will shutdown after waiting the number of Wait Days Before, then for the nuber of Shut Down Days, for either workdays or ALLDays, which disregards whether the day is currently on or off in the calendar. This table is only used if the checkbox below under Calculate Timing Information is checked and does not permanently modify the calendar unless you check Generate Debug info then you have the option to save the calendar at the end of timing. |
|
|
|
|
|
|
|
|
|
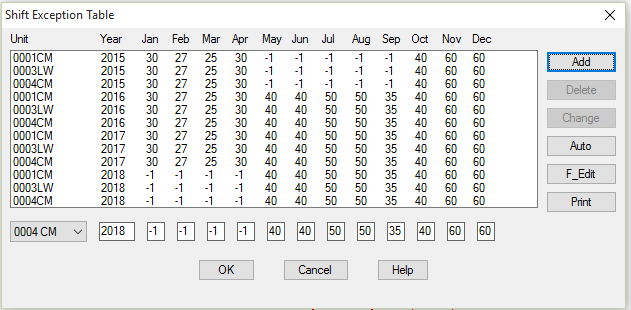 |
|
|
|
|
The above table overrides shifts in the calendar and area files. The -1 means use the shifts for the area, if they exist, otherwise use the calendar. |
|
|
|
|
|
|
|
|
|
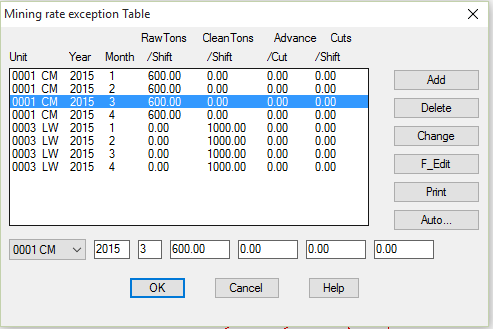 |
|
|
|
|
The above Mining Rate Exception table overrides any mining rates in the Machine Sequence File or the mining rate multipler in the Area file for the month and year specified. The Auto button makes it quick and easy to add these. |
|
|
|
|
|
|
|
|
|
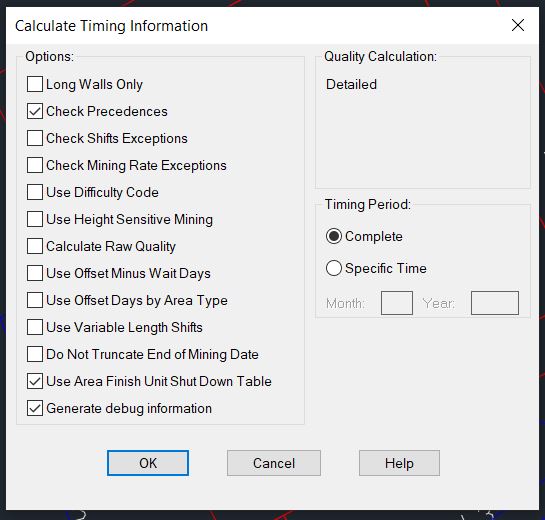 |
|
|
|
|
Above you can see the many options that can be invoked to calculate the timing information. |
|
|
|
|
|
|
|
|
|
Mapping & Reporting Features |
|
|
|
|
The simulated mining module creates a master production data file which is the basis for maps and reports by time period (fiscal or calendar year), area and/or machine. Production can also be reported by surface or mineral lease. The graphical schedule output includes color coded timing maps by month,quarter, year, machine, area or quality. A suite of standard reports are provided but the master production data is also exported in spreadsheet compatible files for creating custom reports. A sample timing map is show below. The system also has various functions for solid fill, coloring, dates and other timing map cosmetics. |
|
|
|
|
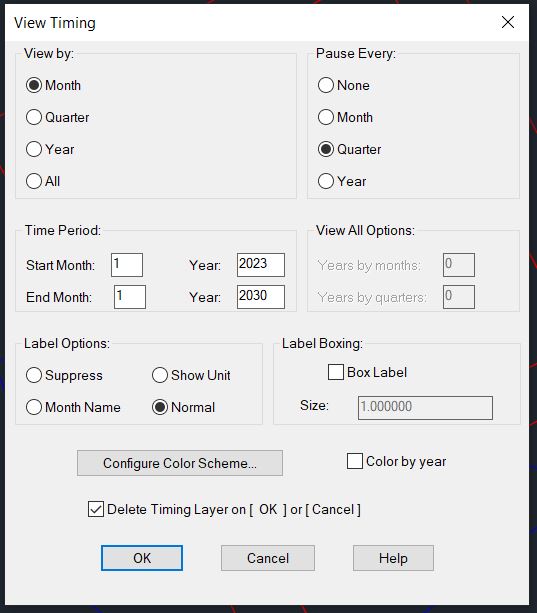 |
|
|
|
|
The above is Quick View Timing with a simple interface the map below shows the output. |
|
|
|
|
|
|
|
|
|
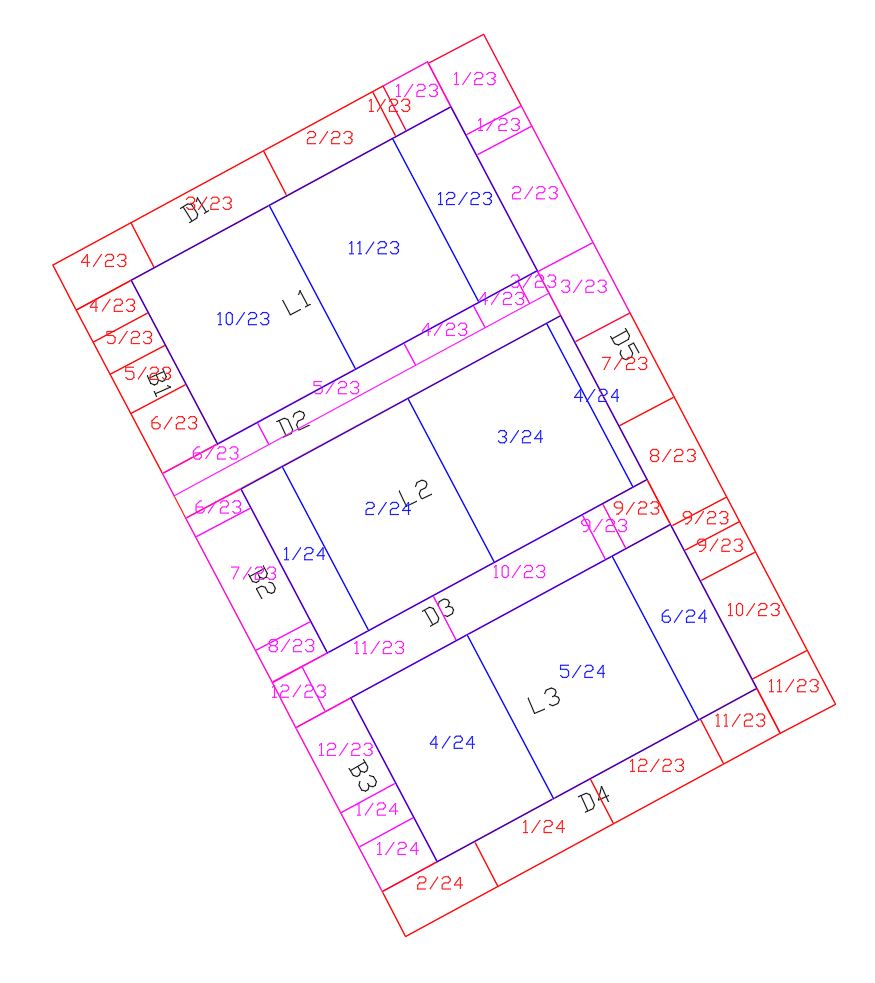 |
|
|
|
|
The above is the sample output if Quick View Timing. The size of the dates and such can be changed in Boundary/Text Size.. |
|
|
|
|
|
|
|
|
|
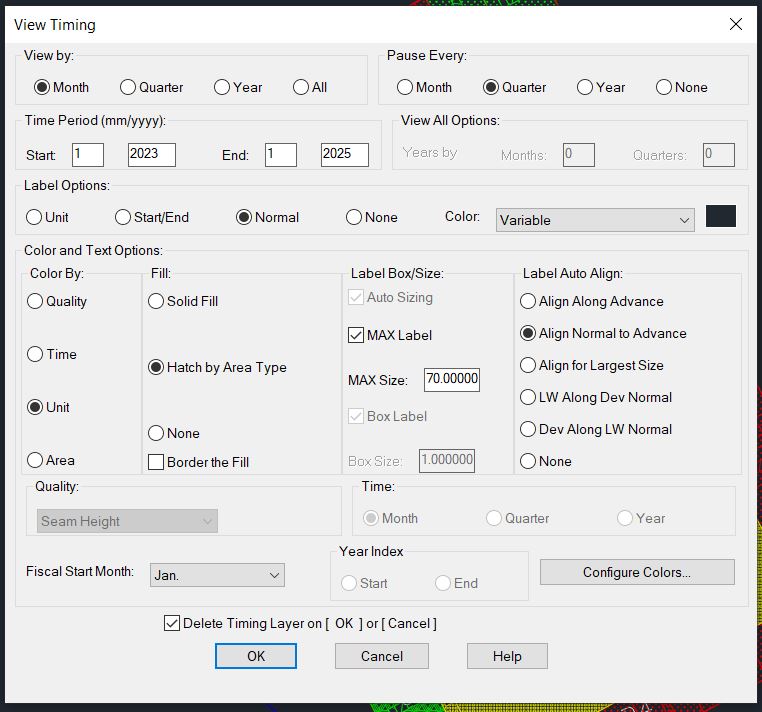 |
|
|
|
|
Above is the Detailed View Timing with many features and options. Below are some scenarios. |
|
|
|
|
|
|
|
|
|
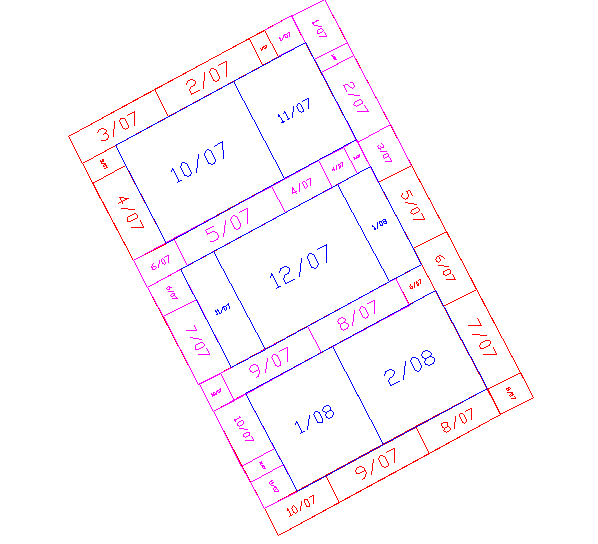 |
|
|
|
|
|
|
|
|
|
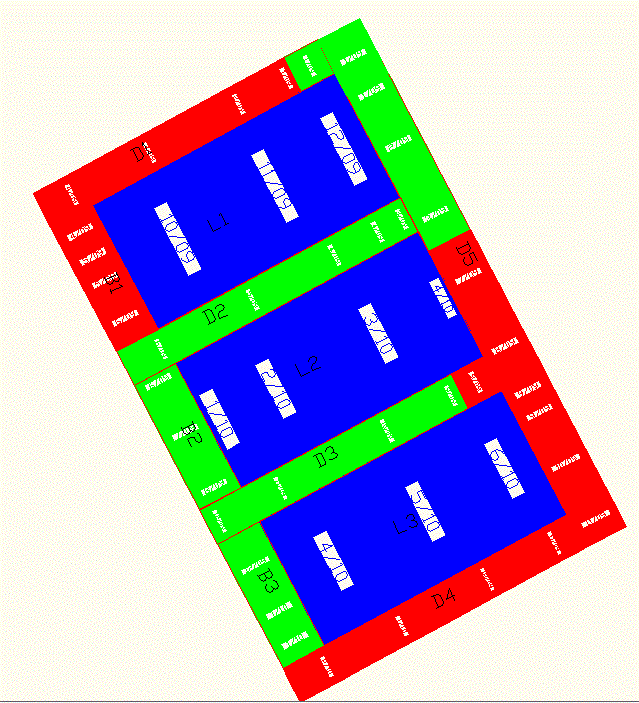 |
|
|
|
|
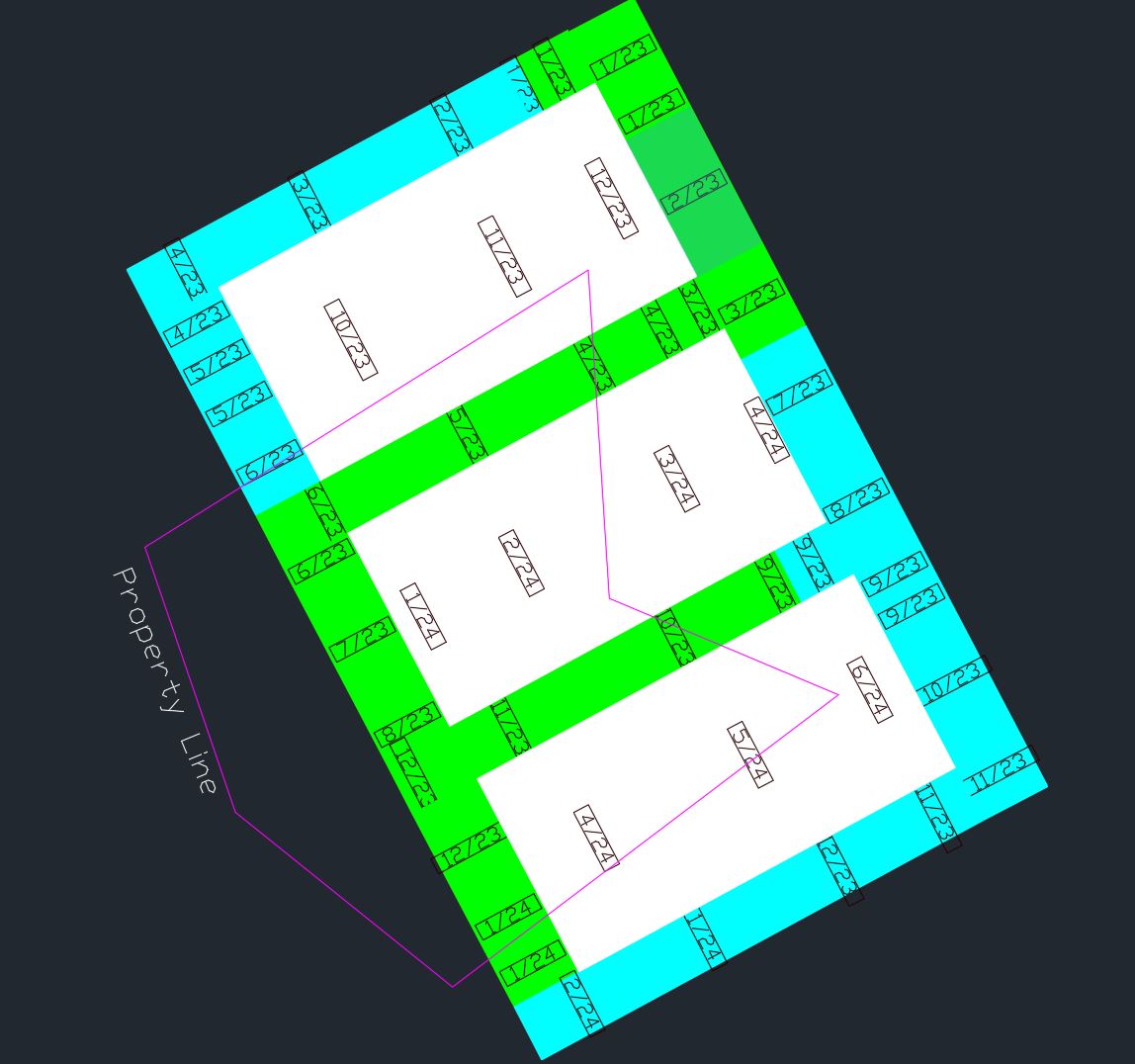 |
|
|
|
|
Above timing map with solid fill can color by Unit, Time, Area or Quality. Also shows Property line for Royalty Reports. |
|
|
|
|
|
|
|
|
|
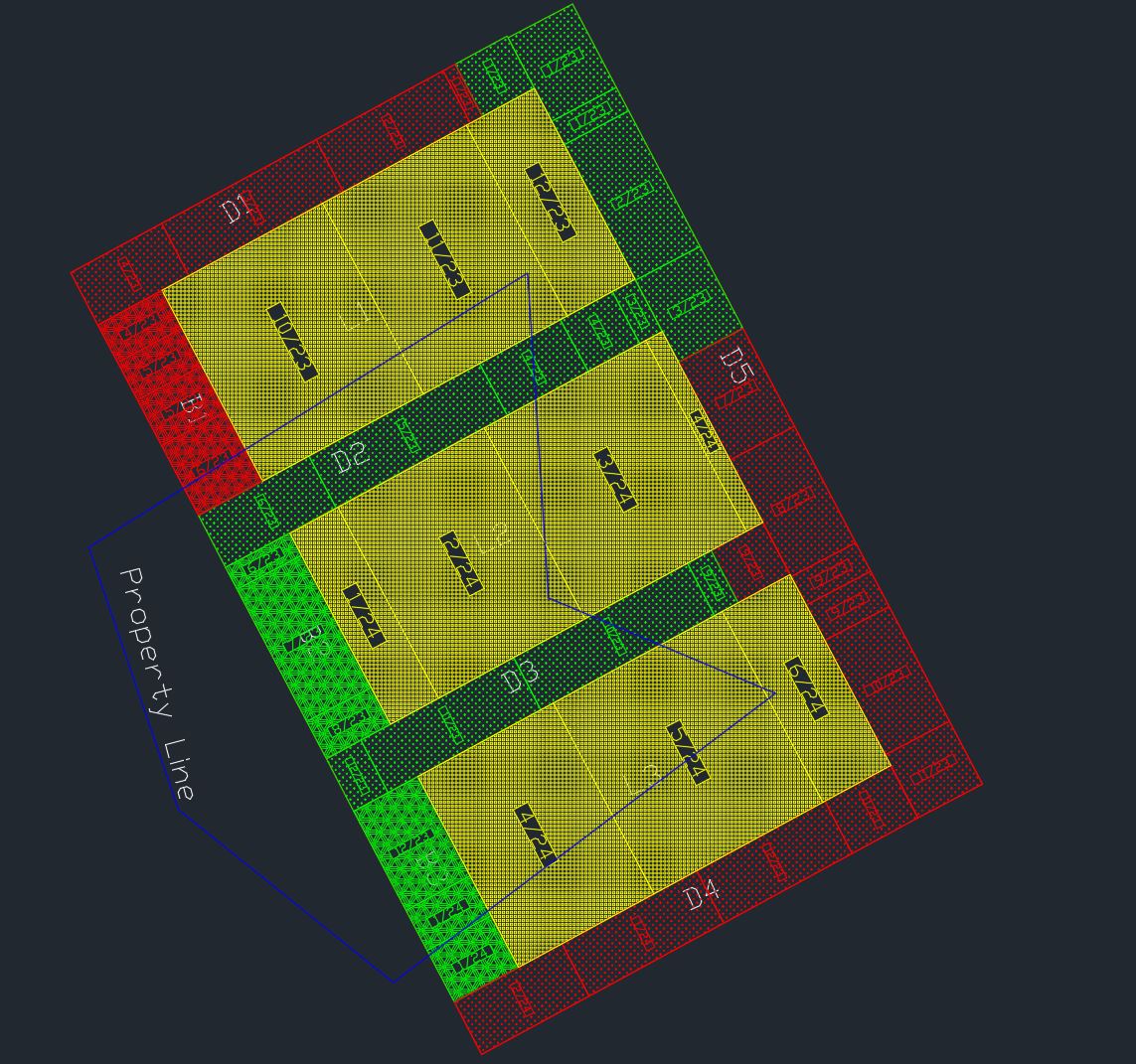 |
|
|
|
|
Above timing map with hatch fill can color by Unit, Time, Area or Qualtiy and change the hatch pattern. Also shows Property line for Royalty Reports. |
|
|
|
|
|
|
|
|
|
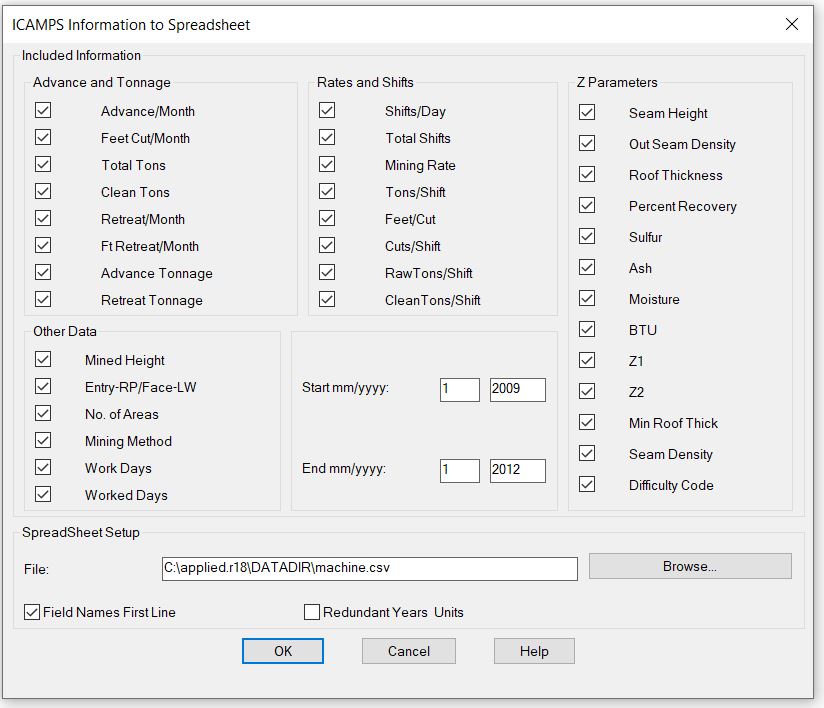 |
|
|
|
|
Above is one of the more popular reports that exports a comma seperated file to any spreadsheet that reads comma seperated files. |
|
|
|
|
|
|
|
|
|
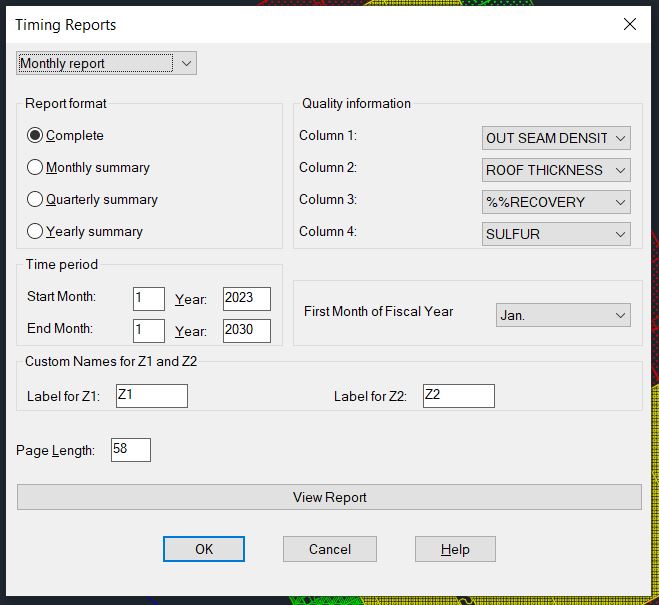 |
|
|
|
|
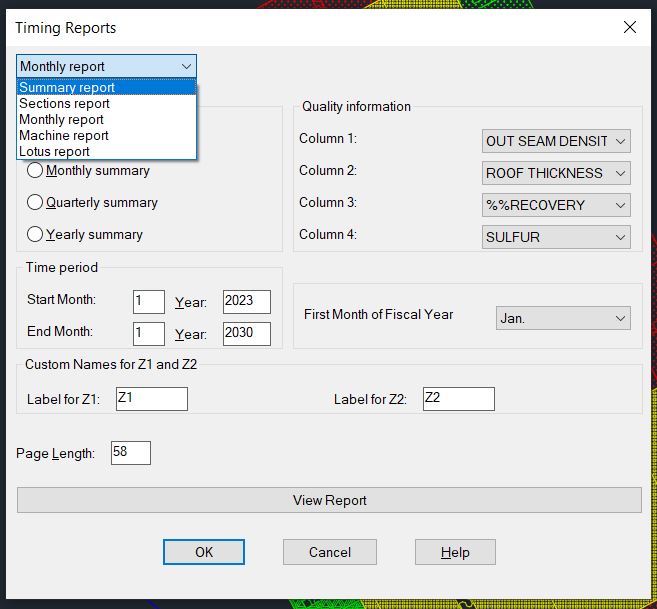 |
|
|
|
|
Standard MineSimU reports can be viewed in an editor, printed to a text file, or printed. |
|
|
|
|
|
|
|
|
|
Cost Reporting Features |
|
|
|
|
The system generates cost estimates for budget purposes with spreadsheet software.To estimate future royalty payments, timing maps are matched against property lines. The output consists of production and quality reports by lessor, time period and/or type of mining.
The bills of labor and material and other cost related information from the mining areas file and the master production output file are read into a spreadsheet to create estimates of labor, material and equipment requirements by time period, mining type or other user selected criteria. The royalty, labor and material requirements are then extended at user specified prices to prepare budgets. |
|
|
|
|
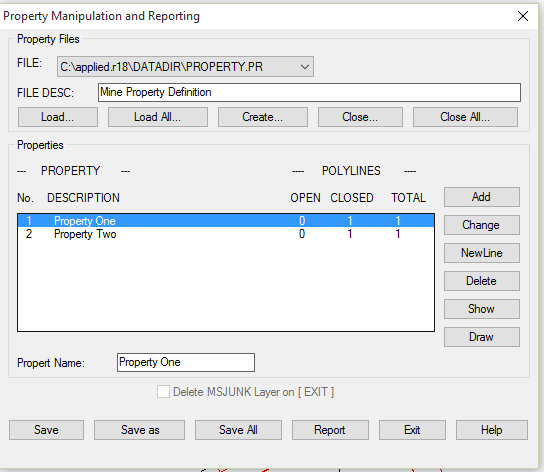 |
|
|
|
|
|
|
|
|
|
Main MineSimU Menus. There are a few others that are mostly helpful AutoCAD menus. |
|
|
|
|
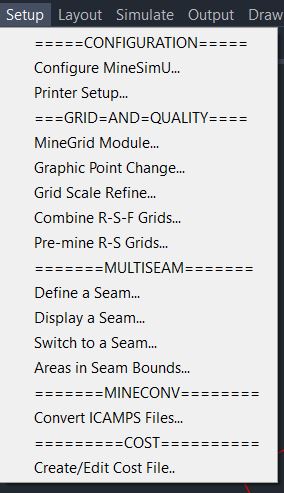 |
|
|
|
|
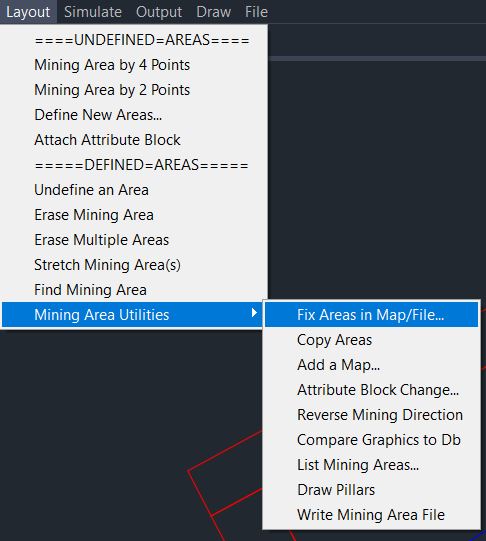 |
|
|
|
|
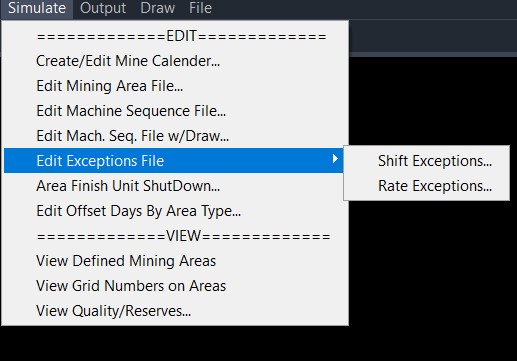 |
|
|
|
|
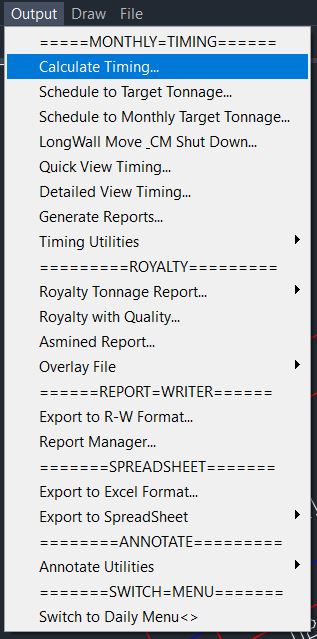 |
|
|
|
|
Summary of MineSimU Features
- AutoCAD Application, runs inside AutoCAD
- Windows Dialog Box Interface
- Geological and Quality Data Analysis
- Automated Calendar Creation
- Mine Layouts in AutoCAD
- Retreat Mining
- Sub-Divided Areas
- Detailed Mine Sequencing
- Mining Simulations
- Comprehensive Mapping and Reporting
- Cost and Resource Reporting
- Development, Bleeder and Longwalls
- Calculate Percent Extraction
- Up to 20 Grids and 20 Calendars
- Seam Height Sensitive Mining
- Adjust Rate for Difficult Conditions
- Many Grid manipulation functions
- Displace Grid
- Change points in Grid selecting the area of the grid to change
- Grid Scale Refinement
- Combine Roof-Seam-Floor Grids
- Pre-Mine Roof - Seam Grids
- 14 Grid/Quality Parameters per Grid, 2 user defined
- Quality Calculations can be Approximate, Detailed or Complex
- Custom Name Quality/Grid Parameters
- 3 ways to handle Out of Seam Dilution (roof/floor, min mining height, or grid)
- Multiple Seam Support
- Stretch Mining Areas
- Many Ways to Manipulate Shifts (by month exceptions, area, or calendar days)
- Many Ways to Manipulate Rates (by month exceptions, area, or machine and more)
- Find Mining Area
- Copy Areas
- Add/Combine Maps
- Draw Pillars
- Mark Holidays in Calendar
- View Grid/Quality Info on Drawing
- Monthly Timing and Daily Timing
- Schedule To Target Tonnage
- Longwall Move Features marks days in calendars
- Area Finish Unit Shutdown any mahines when area finishes
- Many Options to View Timing Maps
- Machine Change Outs
- List Miner Unit Delays
- Royalty Tonnage Reports
- Many Spreadsheet Reports
- Export Area File
- Export Timing File
- Export Combined File
- Export Machine Data
- Report Writer Support
- Much more..............
|
|
|
|
|
|
|
|
|
|
|
|
|
|